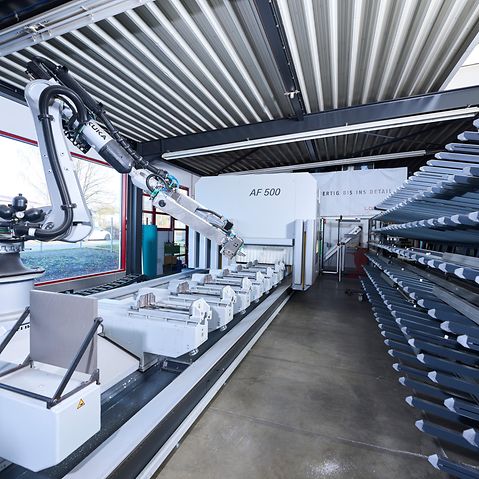
Automation technology
Automation technology – five benefits of automation for your business
It's no secret that there is a lack of workers in many industries. As if that wasn't enough cause for worry, many workers are set to retire in the next ten years and take their special skills, knowledge and experience with them. Technology and automation have the potential to massively change this process and therefore offer enormous opportunities for your company.
All processes and work equipment that enable production processes and systems to be carried out automatically are known as automation technology. As a result of this, human intervention in production automation is minimal in Industry 4.0. The goal of automation technology is to ensure that systems and machines are able to carry out work processes independently, efficiently and with minimal errors. Different degrees of automation are possible for different systems according to complexity. The higher the degree of automation, the lower the amount of human intervention required to manage processes.
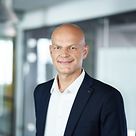
"The introduction of automation technology is a decisive checkpoint on our path towards Industry 4.0. Automation offers significant benefits, particularly in light of challenges such as demographic change and the lack of skilled workers."
Olaf Pantel, Head of Fabrication Products, Schüco International KG
The five most important benefits of automation technology for the metal fabricator
Growing demand and the increasing skills gap in the industry is causing metal fabricators to search for ways to improve efficiency and product quality.
The use of automation technology offers many important advantages.
1. Better data access
Modern, automated machines are equipped with sensors and software which record a large amount of relevant data, such as the work performed, the timeframe in which a task was completed, and the machine's performance when carrying out the task. These sensors can collect lots of information about the system processes and work processes.
The advantages are clear: work is more efficient, tasks can be planned more precisely and customers receive better cost estimates.
2. Improved quality
One of the most remarkable benefits of automation is the improved quality of the fabricated products. Machines can carry out tasks often with a minimal error rate.
Human employees can solve problems and adapt to new work conditions, which robots can't. However, their performance is not the same as that of robots. Consistency in the metal fabrication industry is very important.
Improved efficiency and quality
One of the most important benefits of automation technology is improved efficiency. Robots are often more efficient than human labour and can complete two to three times more work in the same amount of time. They can also complete tasks with fewer fluctuations in quality.
Thanks to this improved efficiency, fabricators can complete more tasks with the same numbers of staff and resources. This is particularly beneficial when the job market is strained and customer demand is high.
4. Prevention of fatigue
Most automation solutions are designed to complete tasks which fall under the following categories:
● dangerous
● dirty
● monotonous
These kinds of tasks are ideal for automation as they are either dangerous for human employees to carry out or reduce their productivity. Automation also helps to prevent human employees from carrying out repetitive movements, which can negatively impact health.
5. Guaranteed safety
Many modern machines have sophisticated safety mechanisms which reduce the risks for those involved in their operation. The elimination of monotonous work processes minimises fatigue for employees over longer periods of time. Studies have shown that fatigue at the workplace has a significant impact: 13% of safety problems can be traced back to tired and overexerted employees. The prevention of fatigue is a big step towards greater safety.
More information on automation technology
The definition of automation technology
The definition of automation technology
"Automation technology" refers to machines that complete tasks previously carried out by humans or, increasingly, tasks that could otherwise not be completed. Automation is an area of electrical engineering concerned with the automated operation of production systems. Due to the many benefits automation technology offers for businesses, it is currently used in numerous industries and particularly in the area of metal fabrication. The terms "industrial automation" and "production automation" involve the integration of devices in a self-managed system. Automation technology can revolutionise entire industries and affects almost all aspects of modern life.
When is it worth investing in automation technology?
When is it worth investing in automation technology?
The use of systems which automate fabrication offers many benefits.
Firstly, automation technology frees people from carrying out potentially dangerous and physically exerting tasks. Machines can take on routine tasks. It is no wonder that technological advancements go hand in hand with population growth. The increasing population numbers mean the demand for high-quality products is also growing and mass production is required.
Machines can also guarantee a consistently high performance and are more efficient than manual labour.
Finally, automation improves product quality and simultaneously reduces labour costs.
The different levels of automation
The different levels of automation
Automated systems can come into use in the many different levels of production processes in the area of automated fabrication. The classic production machine is the most well known example of automation.
The CNC machine tool (Computerised Numerical Control) is an example of an automated system which manages various control systems. A CNC machine is typically part of a more comprehensive fabrication system which can also be automated.
There are four levels in the automation pyramidof a production system.
- Device level: The device level is the bottom level of the automation pyramid. It comprises actuators, sensors and other hardware machine components. The individual control loops of the machine, such as the control loop for an axis of a CNC machine or the hinge of an industrial robot, are combined with the devices.
- Machine level: Individual machines are constructed out of hardware components on the device level. Some examples are CNC machine tools and other fabrication systems, industrial robots, motorised conveyor belts and driverless transport systems.
- Workshop level: This level involves the factory or production systems. It receives instructions from the operational information system and implements these in the operational production plans.
- Company level: The company information system is at the top of the automation pyramid. The company level is responsible for all company management tasks, including sales, marketing, bookkeeping, construction, research, general planning and production planning.