When architects build their own homes

When architects build their own homes
Some architects want to build their own home because it allows them a purity of vision that a commercial project does not. Others might want to pursue a particular technical or design idea. The appeal might lie in the opportunity to explore new materials or pursue new business opportunities. Equally, a self-build project might simply be an chance to get hands-on with the construction process.
Whatever the reason, the Schüco/Architecture Today webinar showcases three of the most exciting new homes around.
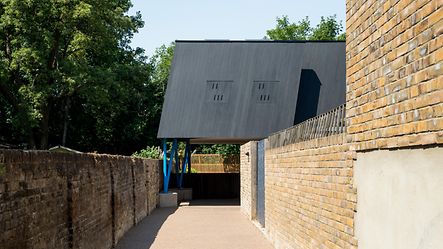
Backwater by Patrick Michell of Platform 5 Architects
Backwater by Patrick Michell of Platform 5 Architects
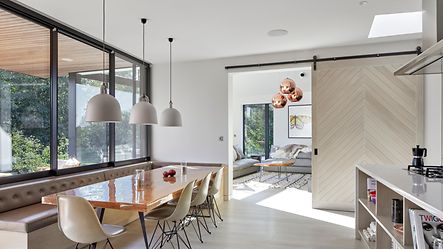
Backwater was designed by Patrick Michell of Platform 5 Architects as both a holiday home for his family and as a holiday let business. As such, the project's budget was developed based on a business plan and estimated rental rates and occupancy levels. The project "had to wash its face financially", says Michell.
Michell found a site in the Norfolk Broads on the bank of a private lagoon connected to the wider broads. The site was originally occupied by a timber-framed bungalow built in the 1950s on timber piles. The piles were now rotten and the house was sinking into the ground so the planners were keen to see the building replaced.
Michell's replacement scheme draws on the Broads' waterfront vernacular of pitched-roof buildings. He translated this into his design for a house with three bays: one for living, one for eating and one for sleeping.
The bays taper: they are narrow on the northern elevation where they face the land and wider on the southern elevation overlooking the lagoon. To minimise solar gains on the southern elevation, the roof overhangs both the living and eating bays to form a large, sheltered veranda.
One of the biggest design challenges was dealing with the site itself. The structural engineer described the ground as "reinforced water". Unsurprisingly, the bungalow that had previously occupied the site flooded in winter.
To ensure this does not happen with Backwater, Michell has raised the building 1.2 metres above the ground, high enough to cope with even the most extreme flood (including the predicted 100-year rise in sea level).
To hold the house aloft, Backwater is supported on a series of 10 metre-deep steel piles which pass through a 4 metre layer of peat to the solid ground beneath. The piles support a galvanised steel sub-frame on which the timber frame house is built. In fact, ground conditions were so bad that even the timber decking surrounding the house had to be supported on piles.
For the main contractor, the challenging ground conditions meant that heavy vehicles were unable to access the site so all components had to be small and light enough to be transported to site by van. "Everything had to be designed to be lightweight and simple," says Michell.
Once the bungalow had been demolished the contractor commenced piling, just as the site suffered autumn flooding. "It was difficult to set out the piles with no firm reference points, which meant we had to re-pile a number of them," says Michell. The high water levels meant that the contractor even had to peg down the wooden formwork used to cast the pile caps to prevent it floating away.
The challenging site meant that it took six difficult months to install the piles. Once they were in place, just one week was needed to bolt together the prefabricated galvanised steel supporting frame on which the house stands. Joists were then added to the steel frame to create a working platform from which the contractor was able to assemble the timber frame elements of the house. The completed dwelling is clad with timber shingles.
The finished result is a restrained, contemporary family holiday home and desirable holiday let which opens out to the water, taking full advantage of its magnificent location.
Pitched Black by Rhys Cannon at Gruff Architects
Pitched Black by Rhys Cannon at Gruff Architects
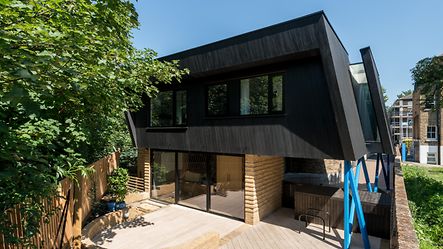
Rhys Cannon, a Director at Gruff Architects, and his family moved into his self-built home in Brockley, south-east London, six months ago.
He says it was not his intention to tackle a self-build project but when the opportunity came along to buy a former builder's yard, the plot was "too good to miss".
This is a difficult site: it is quite a small plot on which to position a four-bed family home. The land is also situated on top of a railway cutting behind a row of houses; the only access is down a narrow track.
Cannon's design for his three-level home works hard to tease every millimetre of space from the plot. The basement, ground floor and first floor are all different sizes and constructed using different building methods. This, he says, made developing the details between elements more of a challenge, particularly when it came to ensuring the envelope was airtight. "It gave us lots of headaches," he says.
The first floor of the house is inclined towards the railway track and away from the neighbours. There are no windows on the elevations closest to the adjacent dwellings; all the neighbours can see is the building's eponymous pitched black roof. Cannon has allowed light to enter through slotted windows concealed in the staggered junctions in the segmented roof plane.
A steel frame supports the first floor structure. It overhangs the ground floor at one end of the building, where it is supported on two slender steel legs. A car turntable is located beneath the overhang at the throat of the access track.
The ground floor is constructed from a traditional load-bearing masonry cavity wall. The basement is a concrete construction, its walls formed from contiguous piles with a sprayed concrete inner liner.
Cannon says the basement was a costly construction element. However, because the weight of the building had to be transferred below the level of the railway, extensive ground works were needed in any case. The basement adds to the space significantly. "Had we not done this, it would not have been feasible as a family home," he says.
One of the benefits of designing and building your own home is that "you can take your time and think about details," Cannon says.
He designed and built the formwork, for example, in order to cast the concrete protective base that protects the building's steel legs. He also designed the gully covers. Cannon believes that when you are being creative, you sometimes have to accept that you will make mistakes. For example, there is a drainage gully that is misaligned with a gully he cast in the concrete base. "It reminds us that we made the building," he says. “The fact that we have been able to craft and make elements and have a bit of fun is really important.”
Externally, the building is clad in matt-black painted timber, which is what gives it a looming presence at the end of the narrow access road. Presumably, it is also why Cannon came up with the building's name.
Cork House by Dido Milne and Matthew Barnet Howland of CSK architects
Cork House by Dido Milne and Matthew Barnet Howland of CSK architects

Dido Milne and Matthew Barnett Howland of CSK architects self-built their first house over 20 years ago. It was on a tiny site in Brick Lane which they had bought at auction.
"We learnt the first rule of the self-builder, which is that it will definitely take much longer to complete than we thought," Milne says. She does, however, say that the experience was invaluable in terms of being a developer-architect-occupier.
The site of the pair's second self-build – Cork House – was far less restrictive since it is in the garden of the family's home in Eton. For this project, the pair set out to develop a simple building envelope using only blocks of expanded cork to replace more conventional layered methods of constructing the building's envelope.
Their self-build construction system was assembled by simply placing one block of cork on top of another without the need for additional materials. "Stone and cork both only work in compression, but cork has a lower thermal conductivity," says Milne. She describes the system as "giant plant-based lego".
In order to develop the self-build cork system the architects embarked on 6-year research project, which included three self-builds of increasing scale and complexity.
The first of these built in the pair's garden was the Casket – a shed-sized space. To shape the cork blocks for this, Matthew Barnett Howland, who is also a tutor at the Bartlett School of Architecture, was able to use the school's workshop and milling machines.
Barnett Howland assembled the building from cork blocks held together with timber dowels and lime mortar. The completed building showed cork blocks had promise as a building material, but the dowel and mortar "introduced complexity during construction".
The pair's second prototype built in their garden was Cork Cabin. The research to build this larger prototype was part funded by Innovate UK, EPSRC and industry partners. For this scheme Barnett Howland used blocks of milled cork incorporating a tongue and groove interference fit, which allowed the walls to be built using solid lightweight cork blocks without glue.
"During the design process for the Cabin, we worked out a lot of the principles that we used for Cork House," explains Barnett Howland. These included the use of a raised perimeter beam made from cross-laminated timber (CLT) and insulated using cork as well as a rooflight used as a weight to hold the top few courses of the roof in place.
The Cabin was also useful for the in-situ testing of the wall's thermal performance and the structure's airtightness. The tests showed that, in order to comply with building regulations for airtightness, an expanding tape was needed to seal the joints between blocks. The wall's thermal performance gave a U value of 0.11 W/m2/K.
In addition, the University of Bath tested the structural performance of the cork for compression, shear, creep and out-of-plane loads, allowing engineering firm Arup to demonstrate that the scheme complied with building regulations.
Importantly, the roof was also fire-tested at the BRE for flashover and structural integrity.
"The tests showed that cork behaves in a similar way to CLT, in that it self chars," says Barnett Howland. Following the test, Arup developed a fire-engineered solution for the timber building using sprinklers to comply with building regulations.
Finally, the structure was tested for resistance to driving rain. The cork walls performed well but that the cork roof allowed water ingress. This was resolved using a system of cedar weather boards screwed to the cork corbels.
The Cabin was made and assembled at the Bartlett, then taken apart and reassembled by Barnett Howland, proving that the system could be dismantled at the end of its life.
Having established the construction principles, the duo moved on to the final and largest build – Cork House. This is a linear house consisting of five rooms, each crowned by a pyramid roof and topped with a glass skylight.
Cork House was built using a prefabricated kit, including screw pile foundations, a solid timber platform for the floor and to support the cork wall blocks, a timber ring beam at eaves level, and a solid cork block roof and rooflight topping each roof pyramid.
The 480 mm thick perimeter wall of cork is designed to carry all of the structure's vertical compression loads. Lateral stability is provided by two CLT wardrobes, located in the middle of the building, which are tied to the ring beam at eaves level.
Cork House shows what can be done with a self-build if you can secure a research grant and the resources of Arup, BRE, the University of Bath and the Bartlett's workshops to precision-cut the cork blocks. While few self-builders will have access to these, they can at least draw inspiration from the project.
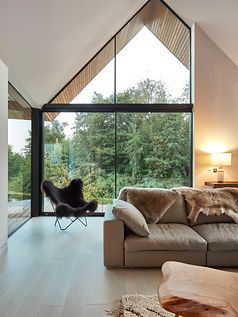
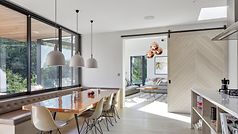
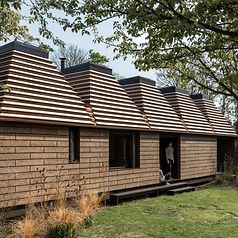
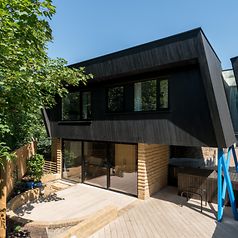
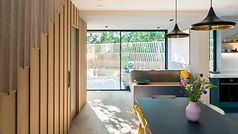
- Work material (e.g. tender specifications, BIM objects, CAD data, catalogues)
- Note content
- Direct contact to Schüco